Designing a product is only half the journey. The other half? Making sure it actually works in the real world. That’s where SolidWorks Simulation shines—a fully integrated analysis tool that allows engineers to test their designs under real-world forces like stress, heat, vibration, and motion without ever building a prototype.
If you’re new to computer-aided engineering, this guide will walk you through everything you need to know to start using SolidWorks Simulation, from basic static analysis to advanced motion and thermal studies.
Table of Contents
What is SolidWorks Simulation?
SolidWorks Simulation is a built-in FEA (Finite Element Analysis) tool used to test and validate 3D models. It helps answer questions like:
- Will this part break under load?
- How much will it deflect or deform?
- Is this design over-engineered?
- How does temperature affect my component?
- How do moving parts interact?
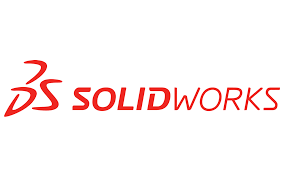
All of this is done inside the SolidWorks interface, using your native CAD files—no exporting needed.
Why Use SolidWorks Simulation?
✅ Validate your designs before prototyping
✅ Reduce material usage and cost
✅ Identify weak points early in the design process
✅ Speed up time-to-market
✅ Meet industry safety and compliance standards
It’s like having a virtual test lab right on your desktop.
Types of Simulation Studies in SolidWorks
Study Type | What It Tests |
---|---|
Static | Stress, strain, and displacement |
Thermal | Temperature effects and heat transfer |
Frequency | Resonant modes and vibration response |
Buckling | Load capacity before sudden failure |
Drop Test | Impact and shock loading |
Fatigue | Life cycle prediction under repeated loads |
Motion Analysis | Moving assemblies and time-based forces |
Nonlinear | Material plasticity and large deformation |
Optimization | Automated design improvement |
SolidWorks Simulation Add-Ins Explained
- SimulationXpress (Free): For quick static stress analysis on individual parts
- SolidWorks Simulation Standard: Basic FEA, fatigue, motion
- Simulation Professional: Thermal, buckling, frequency, optimization
- Simulation Premium: Nonlinear, dynamic, advanced capabilities
Tip: You can activate Simulation via Tools > Add-Ins > SolidWorks Simulation
.
How to Run a Basic Simulation in SolidWorks
Let’s run a simple static stress analysis on a part:
Step 1: Activate Simulation
- Go to
Tools > Add-Ins
- Check the SolidWorks Simulation box
Step 2: Set Up a Study
Simulation > New Study > Static
- Name your study and click OK
Step 3: Apply Materials
- Right-click on the part in the Simulation Tree
- Choose Apply/Edit Material
- Select from the built-in library (e.g., Aluminum 6061)
Step 4: Add Fixtures (Supports)
- Define how the part is held or constrained (e.g., fixed face, hinge)
Step 5: Apply Loads
- Add forces or pressures to simulate real-world use
- Direction and magnitude must be defined
Step 6: Mesh the Model
- Right-click
Mesh > Create Mesh
- Choose mesh density (finer for precision, coarser for speed)
Step 7: Run the Simulation
- Click
Run
- View results: stress, displacement, strain, and factor of safety
Understanding Simulation Results
Result Type | What It Means |
---|---|
Von Mises Stress | Used to determine yielding of materials |
Displacement | How far the part bends or moves |
Strain | Percentage of deformation |
Factor of Safety | Ratio of strength to applied stress |
Tip: Use the Probe Tool to examine stress at specific locations.
Using Simulation in Assemblies
- Add contacts between parts (bonded, no penetration, etc.)
- Define connections like bolts or pins
- Apply motion loads and constraints
Use Motion Study to simulate real movement (e.g., gear rotation, robotic arm).
Thermal and Fluid Simulations
- Thermal Analysis: Apply heat sources, conductivities, and convection coefficients
- Flow Simulation (requires separate module): Analyze airflow, cooling, and pressure
You can simulate:
- Electronics overheating
- Heat sink performance
- Pressure drop in piping systems
Tips to Improve Simulation Accuracy
✅ Always apply correct units and materials
✅ Start with coarse mesh, then refine
✅ Use symmetry to reduce model size
✅ Apply realistic boundary conditions
✅ Validate with hand calculations where possible
✅ Interpret results critically—simulation is a tool, not truth
Common Mistakes to Avoid
❌ No constraints → model floats in space
❌ Over-constraining → unrealistically stiff system
❌ Wrong material properties → incorrect stress/strain
❌ Tiny mesh → long runtimes, potential crashes
❌ Misaligned loads → unrealistic deformation patterns
Best Use Cases for SolidWorks Simulation
- Load-bearing mechanical parts
- Sheet metal components
- Plastic housing with snap-fit features
- Assemblies under moving loads
- Heat dissipation in electronics
- Structural components under wind or snow loads
FAQs
Is SolidWorks Simulation easy to learn?
Yes. Start with Static Studies and use SimulationXpress for part-level analysis before exploring complex simulations.
Do I need Simulation Premium to run real tests?
Simulation Standard covers most beginner and intermediate needs. Premium is for nonlinear or dynamic studies.
Is the simulation accurate?
Yes—when set up correctly. Use proper meshing, real-world constraints, and validated materials for reliable results.
Can I simulate drop impact or explosions?
Drop tests are available in Simulation Professional. Explosive/dynamic simulations require third-party or specialized tools.
Is SimulationXpress enough for beginners?
It’s a great starting point, but very limited. You’ll quickly outgrow it and want Simulation Standard or higher.
Conclusion: Bring Your CAD to Life with SolidWorks Simulation
SolidWorks Simulation transforms your 3D models from digital drafts into engineered solutions. With the ability to test, validate, and optimize without leaving your CAD environment, Simulation helps reduce risk, increase performance, and build better products—faster.
Whether you’re designing a simple bracket or a complex machine, virtual testing is your competitive edge. Start simulating today, and bring real-world thinking into your design process.
Suggested Inbound Links
- SolidWorks for Beginners – Learn the Basics of 3D Modeling
- MySolidWorks Simulation Training
- SolidWorks Forums