Introduction to SolidWorks Routing
In the complex world of product design and manufacturing, the efficient and accurate design of piping and tubing systems is paramount. From industrial machinery and process plants to automotive systems and consumer appliances, fluid conveyance is a critical aspect that demands precision, flexibility, and robust validation. Traditional methods of designing these systems can be time-consuming, prone to errors, and difficult to integrate with the overall product assembly. This is where SolidWorks Routing emerges as an indispensable tool, offering a specialized environment within the SolidWorks ecosystem to streamline the creation, modification, and management of routed systems.
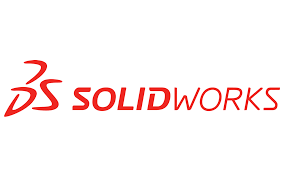
SolidWorks Routing is an add-in module that extends the core capabilities of SolidWorks, providing a powerful suite of tools specifically tailored for the design of piping, tubing, electrical cabling, and conduit systems. It automates many of the tedious tasks associated with routing, such as selecting appropriate fittings, calculating lengths, and ensuring proper connections, thereby significantly reducing design time and minimizing potential errors. By integrating routing directly into the 3D CAD model, designers can ensure that these critical systems fit perfectly within the overall product, avoiding costly interferences and rework during manufacturing.
This comprehensive article will delve deep into the functionalities and benefits of SolidWorks Routing, focusing specifically on its application in piping and tubing design. We will explore its core features, the typical workflow involved, best practices for effective utilization, and the significant advantages it offers to engineers and designers in various industries.
Table of Contents
The Importance of Efficient Piping and Tubing Design
Piping and tubing systems are more than just conduits for fluids; they are intricate networks that often dictate the performance, safety, and maintainability of a product or facility. In industries such as oil and gas, chemical processing, HVAC, automotive, and aerospace, the design of these systems is subject to stringent regulations, performance requirements, and space constraints.
Inefficient design processes can lead to:
- Interference Issues: Clashes between pipes, tubes, and other components, requiring costly redesigns and physical modifications.
- Material Waste: Incorrect length calculations or improper fitting selections leading to scrap.
- Assembly Difficulties: Poorly designed routes making assembly and maintenance challenging.
- Performance Degradation: Incorrect pipe sizing or routing impacting fluid flow and system efficiency.
- Compliance Risks: Failure to meet industry standards and regulatory requirements.
SolidWorks Routing addresses these challenges head-on by providing a robust, intelligent, and integrated design environment that ensures accuracy, optimizes material usage, and facilitates compliance.
Core Features of SolidWorks Routing for Piping and Tubing
SolidWorks Routing is packed with features that simplify and automate the design process. Here are some of the key functionalities relevant to piping and tubing:
1. Automated Route Generation
One of the most powerful features of SolidWorks Routing is its ability to automate the creation of routes. Designers can define a starting point and an end point, and the software can intelligently generate a path, considering obstacles and preferred routing directions. This automation extends to:
- Auto Route: Generates a 3D sketch path between selected connection points.
- Drag and Drop: Users can drag and drop fittings (e.g., elbows, tees, reducers) from a library directly onto the route, and the software automatically adjusts the route and adds the necessary pipe segments.
- Piping Spooling: Allows for the creation of manufacturing spools, breaking down long runs into manageable, fabricable sections.
2. Extensive Component Library
SolidWorks Routing comes with a comprehensive library of standard piping and tubing components, including:
- Pipes and Tubes: Various sizes, materials, and schedules.
- Fittings: Elbows, tees, reducers, flanges, caps, unions, etc.
- Valves: Ball valves, gate valves, check valves, globe valves, etc.
- Gaskets and Fasteners: Essential for complete assembly definition.
Users can also create and add their custom components to this library, ensuring that specific project requirements or proprietary parts are readily available. These components are “smart,” meaning they contain routing-specific information such as connection points, sizes, and flow directions.
3. Intelligent Connection Points (CPoints)
CPoints are crucial for the intelligence of SolidWorks Routing. These are defined points on components that indicate where a pipe or tube can connect. When a component is added to a route, SolidWorks automatically recognizes these CPoints, facilitating quick and accurate connections. This feature eliminates the need for manual alignment and ensures that all connections are geometrically correct.
4. Automatic Bill of Materials (BOM) Generation
As the routing design progresses, SolidWorks automatically updates the Bill of Materials. This BOM includes all pipes, tubes, fittings, valves, and other components used in the route, along with their quantities, lengths, and other relevant properties. This real-time BOM generation is invaluable for cost estimation, procurement, and manufacturing planning, significantly reducing the risk of material shortages or excesses.
5. Design Rule Checking and Interference Detection
SolidWorks Routing integrates seamlessly with SolidWorks’ powerful interference detection capabilities. As routes are created, the software can highlight potential clashes with other components in the assembly, allowing designers to resolve issues early in the design cycle. Furthermore, design rules can be set up to ensure compliance with specific standards, such as minimum bend radii for tubes or required clearances around components.
6. Flexible and Rigid Tubing Support
The module supports both rigid piping and flexible tubing. For flexible tubing, it allows designers to define bend radii and ensures that the tubing adheres to these constraints, providing realistic representations and preventing over-bending.
7. Walk-Through and Exploded Views
The ability to create walk-through animations and exploded views of the routed system helps in visualizing the design, identifying potential assembly challenges, and communicating the design intent more effectively to stakeholders.
The SolidWorks Routing Workflow for Piping and Tubing
A typical workflow for designing piping and tubing systems in SolidWorks Routing involves several key steps:
Step 1: Preparing the Assembly
Before starting the routing process, the main assembly where the piping or tubing will reside needs to be prepared. This involves placing all relevant equipment, tanks, pumps, and other components that will connect to the routed system. Ensure that these components have defined connection points (CPoints) if they are custom parts, or utilize the CPoints of standard library components.
Step 2: Initiating a New Route
A new route can be initiated from a specific connection point on an existing component or from a blank sketch. SolidWorks Routing typically opens a sub-assembly for the route, keeping the main assembly clean and organized.
Step 3: Defining the Route Path
This is the core of the routing process. Designers can use various methods to define the path:
- Sketching: Manually sketching the 3D path using lines, arcs, and splines. SolidWorks’ 3D sketch tools are highly intuitive for this.
- Auto Route: As mentioned, this feature intelligently generates a path between two selected CPoints.
- Drag and Drop: Dragging and dropping fittings like elbows automatically creates segments of the route.
- From-To List: For complex systems, a “from-to” list can be used to define connections, and SolidWorks can attempt to route them.
As the path is defined, SolidWorks Routing automatically inserts the necessary pipe or tube segments.
Step 4: Adding Components (Fittings, Valves, etc.)
Once the basic path is established, fittings, valves, and other inline components are added. When a fitting is dragged onto the route, SolidWorks intelligently snaps it into place, adjusting the surrounding pipe segments as needed. For example, dropping an elbow onto a straight pipe segment will automatically split the segment and insert the elbow, maintaining connectivity.
Step 5: Modifying and Optimizing the Route
Routes are rarely perfect on the first attempt. SolidWorks Routing provides robust tools for modification:
- Drag Handles: Easily drag segments of the route to adjust their position.
- Dimensioning: Use smart dimensions to precisely control lengths and offsets.
- Route Splitting: Split long pipe runs into multiple segments for manufacturing or to insert new components.
- Bend Editing: For tubing, adjust bend radii and angles.
- Component Swapping: Easily swap out one fitting for another (e.g., a 45-degree elbow for a 90-degree elbow).
Optimization involves ensuring the most efficient use of space, minimizing pipe lengths, and adhering to design standards.
Step 6: Verifying and Validating the Design
Before finalizing the design, it’s crucial to perform checks:
- Interference Detection: Run a comprehensive interference check against the entire assembly.
- Clearance Verification: Ensure adequate clearance for maintenance and assembly.
- Design Rule Checking: Verify that all defined design rules (e.g., minimum bend radii, slope requirements) are met.
- Pressure Drop Analysis (External Tools): While SolidWorks Routing doesn’t directly perform fluid dynamics simulations, the accurate 3D model it creates can be exported to specialized CAE tools for pressure drop and flow analysis.
Step 7: Generating Documentation
The final step involves generating the necessary documentation for manufacturing and assembly:
- Detailed Drawings: Create 2D drawings of the routed system, including dimensions, annotations, and isometric views.
- Bill of Materials (BOM): Generate a comprehensive BOM for procurement.
- Cut Lists: For piping, generate cut lists specifying the exact lengths of each pipe segment.
- Bend Tables: For tubing, generate bend tables providing precise bending instructions.
Best Practices for Effective SolidWorks Routing
To maximize the benefits of SolidWorks Routing, consider these best practices:
- Plan Ahead: Before diving into the software, have a clear understanding of the system layout, connection points, and any critical constraints. Sketching out the general route on paper can be helpful.
- Utilize the Design Library: Leverage the standard components in the SolidWorks Design Library. For custom parts, create them as routing components with defined CPoints for seamless integration.
- Define CPoints Accurately: The accuracy of CPoints on your custom components is paramount. Incorrect CPoints will lead to misaligned connections and errors.
- Use Sub-Assemblies: SolidWorks Routing automatically creates a sub-assembly for each route, which is good practice. Avoid creating multiple routes directly in the top-level assembly; group related routes into their own sub-assemblies for better organization.
- Employ 3D Sketching Effectively: Master the 3D sketch tools. Using planes, parallel/perpendicular relations, and dimensions in 3D space is key to creating precise routes.
- Regular Interference Checks: Run interference detection frequently, especially after significant modifications, to catch issues early.
- Standardize Components: Where possible, standardize the fittings and components used across projects to streamline the library and improve consistency.
- Leverage Templates: Create routing templates with pre-defined settings, layers, and common components to accelerate new projects.
- Understand Routing Options: Familiarize yourself with the various routing options, such as minimum bend radii, automatic elbow insertion, and segment lengths, to tailor the software’s behavior to your needs.
- Training and Continuous Learning: SolidWorks Routing has a learning curve. Invest in proper training and stay updated with new features and best practices.
Advantages of Using SolidWorks Routing
The adoption of SolidWorks Routing for piping and tubing design offers a multitude of advantages:
- Reduced Design Time: Automation of routing, component insertion, and BOM generation significantly cuts down design hours.
- Increased Accuracy: Intelligent connections, design rule checks, and interference detection minimize errors and rework.
- Improved Design Quality: Ensures optimal routing paths, proper clearances, and adherence to standards, leading to more robust and reliable designs.
- Cost Savings: Reduced material waste due to accurate length calculations and fewer design iterations.
- Enhanced Collaboration: The 3D model provides a clear visual representation, facilitating better communication among design teams, manufacturing, and clients.
- Faster Time-to-Market: Streamlined design processes enable quicker progression from concept to production.
- Better Manufacturability: Detailed drawings, cut lists, and bend tables directly from the 3D model simplify manufacturing and assembly.
- Integrated Workflow: Being an add-in to SolidWorks, it offers a seamless workflow with other SolidWorks modules like SolidWorks Simulation for stress analysis or SolidWorks PDM for data management.
Industry Applications
SolidWorks Routing finds extensive application across a wide range of industries:
- Process & Plant Design: Chemical plants, oil refineries, power generation facilities, where vast networks of pipes are essential.
- HVAC Systems: Designing ducting and piping for heating, ventilation, and air conditioning in buildings.
- Automotive: Fuel lines, brake lines, cooling systems, and exhaust systems.
- Aerospace: Hydraulic lines, fuel lines, and environmental control system tubing.
- Heavy Machinery: Construction equipment, agricultural machinery, and industrial robots with complex hydraulic and pneumatic systems.
- Shipbuilding: Routing systems for propulsion, ballast, and utility lines on marine vessels.
- Medical Devices: Designing intricate fluid paths in medical equipment.
Conclusion
SolidWorks Routing is a powerful and indispensable tool for any organization involved in the design and manufacturing of products with complex piping and tubing systems. By automating tedious tasks, ensuring design accuracy, and providing comprehensive documentation, it empowers engineers to create robust, efficient, and manufacturable designs in a fraction of the time compared to traditional methods. Its seamless integration within the SolidWorks environment further enhances productivity and fosters a collaborative design process.
As industries continue to demand higher levels of precision, efficiency, and compliance, the role of specialized CAD tools like SolidWorks Routing becomes ever more critical. Investing in its capabilities and adopting best practices will undoubtedly lead to significant improvements in design quality, cost reduction, and accelerated product development cycles, ultimately providing a competitive edge in today’s dynamic market. For any designer or engineer dealing with fluid conveyance, mastering SolidWorks Routing is not just an advantage, but a necessity.