In the intricate world of mechanical design, creating static models is only half the battle. Real-world products are rarely static; they move, interact, and perform functions. Understanding these movements, predicting their behavior, and optimizing their performance before physical prototyping is crucial for successful product development. This is where SolidWorks Motion Study emerges as an indispensable tool, offering powerful capabilities for the analysis of movement within assemblies.
SolidWorks Motion Study is a comprehensive suite of tools built directly into the SolidWorks environment, allowing engineers and designers to simulate and analyze the kinematic and dynamic behavior of their designs. From simple animations demonstrating functionality to complex dynamic analyses involving forces, torques, and contacts, Motion Study provides a virtual test bed that saves time, reduces costs, and enhances the quality and reliability of mechanical systems.
This article will delve deep into the realm of SolidWorks Motion Study, exploring its fundamental principles, the different types of analyses it offers, its key components, practical applications across various industries, advanced considerations, and best practices for achieving accurate and insightful results.
Table of Contents
The Essence of Motion Study: Beyond Static Design
Traditional CAD software excels at creating geometrically accurate 3D models. However, these models, by themselves, don’t inherently convey how parts will move relative to each other, how forces will propagate through a mechanism, or what the resulting stresses and vibrations might be. SolidWorks Motion Study bridges this gap by transforming static assemblies into dynamic simulations.
At its core, Motion Study allows users to:
- Visualize Movement: See how components interact and move through their range of motion, identifying potential collisions or interferences.
- Analyze Kinematics: Study the position, velocity, and acceleration of components without considering the forces causing the motion. This is crucial for understanding the geometry of movement.
- Analyze Dynamics: Go a step further by incorporating real-world physics, including forces, torques, gravity, friction, and material properties, to understand the loads, stresses, and power requirements of a mechanism.
- Optimize Performance: Use simulation results to refine designs, reduce wear, improve efficiency, and ensure the mechanism operates as intended under various conditions.
By bringing the design to life virtually, Motion Study enables designers to identify and rectify issues early in the design cycle, long before costly physical prototypes are manufactured.
Types of Motion Studies: From Animation to Advanced Dynamics
SolidWorks Motion Study offers a progressive hierarchy of analysis capabilities, each suited for different levels of complexity and required output:
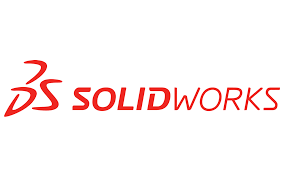
- Animation:
- Purpose: Primarily for visual demonstration and communication. It allows you to create a movie of an assembly’s movement.
- Capabilities: Uses SolidWorks mates to define movement. You can control component positions, camera views, and lighting over time. It does not consider physics or forces.
- Applications: Marketing videos, design reviews, explaining product functionality to non-technical stakeholders, basic interference checking.
- Limitations: No physics-based calculations; movement is purely driven by keyframes and mate controllers.
- Basic Motion:
- Purpose: A lightweight, physics-based simulation for quick checks of assembly movement, interferences, and approximate force reactions.
- Capabilities: Incorporates basic physics such as gravity, springs, dampers, and contact between components. It uses a simplified solver that is computationally efficient.
- Applications: Verifying general mechanism behavior, identifying major interferences, estimating component velocities, and getting a qualitative understanding of forces.
- Limitations: Uses a simplified physics engine, which may not be accurate enough for precise quantitative analysis of forces and stresses, especially in complex systems with many contacts.
- Motion Analysis:
- Purpose: The most powerful and accurate type of motion study, designed for detailed kinematic and dynamic analysis. It uses a robust solver (based on the ADAMS/Solver technology from MSC Software) to provide highly accurate results.
- Capabilities: Includes all Basic Motion features plus advanced physics elements like precise contact modeling (with friction and restitution), external forces (constant, varying, or even imported from FEA results), flexible components (if integrated with SolidWorks Simulation), and robust calculation of reaction forces, torques, power consumption, and energy.
- Applications: Calculating precise loads for component sizing, optimizing cam profiles, designing gear trains, analyzing vibration, predicting wear, and ensuring mechanism durability.
- Limitations: Computationally more intensive, requires careful setup of contacts and forces, and demands a deeper understanding of physics principles for accurate interpretation of results.
Key Components of a Motion Study
Regardless of the type of motion study, several core components are essential for defining and executing a simulation:
- Mates: The foundation of any SolidWorks assembly, mates define the allowed degrees of freedom between components. In Motion Study, these mates are automatically translated into kinematic constraints.
- Motors: Drive the motion of components. You can define rotary motors (e.g., a constant speed motor for a rotating shaft) or linear motors (e.g., a piston moving along a path). Motors can have constant speed, distance, or even advanced functions (e.g., sinusoidal, data points from a file).
- Forces: Apply external loads to components. These can be constant forces, variable forces (e.g., a spring force, a gravitational force), or forces defined by expressions or data.
- Gravity: A crucial environmental factor that applies a constant acceleration to all components in the assembly. You can specify its direction and magnitude.
- Springs and Dampers: Model elastic and damping behaviors between components, essential for understanding energy absorption and vibration.
- Contacts: Define how components interact when they touch. In Basic Motion, contacts are simplified. In Motion Analysis, contacts are highly sophisticated, allowing for definition of material properties (friction, restitution), impact behavior, and precise force transmission.
- Cams: Specialized contacts that define the precise motion of a follower relative to a cam profile, crucial for many mechanical systems.
- Gears and Rack Pinions: Define kinematic relationships between rotating components, ensuring accurate motion transmission.
- Results and Plots: After running a study, SolidWorks generates data that can be plotted. This is where the insights truly emerge. You can plot displacement, velocity, acceleration, forces, torques, power, energy, and more, for any component or point in the assembly.
Practical Applications Across Industries
SolidWorks Motion Study is a versatile tool with applications spanning numerous engineering disciplines:
- Product Design and Development:
- Consumer Products: Analyzing the opening and closing mechanisms of lids, hinges, or retractable components.
- Automotive: Simulating suspension systems, door mechanisms, wiper blades, or engine components.
- Robotics: Analyzing robot arm kinematics, gripper mechanisms, and joint loads.
- Machinery and Automation:
- Manufacturing Equipment: Optimizing cam-driven mechanisms, conveyor systems, and pick-and-place robots.
- Packaging Machinery: Ensuring smooth and efficient product handling, sealing, and cutting operations.
- Agricultural Machinery: Analyzing the movement of tilling equipment, harvesters, or spray booms.
- Biomedical Devices:
- Prosthetics: Simulating joint movement and load distribution.
- Surgical Tools: Analyzing the kinematics and forces involved in instrument operation.
- Heavy Equipment:
- Construction Machinery: Simulating excavator arm movements, bulldozer blade actions, or crane operations.
- Mining Equipment: Analyzing the dynamics of rock crushers or conveyor systems.
In all these scenarios, Motion Study helps engineers to:
- Validate Design Intent: Confirm that the mechanism behaves as envisioned.
- Identify Design Flaws: Detect interferences, excessive loads, or inefficient movements early.
- Optimize Performance: Fine-tune parameters to improve speed, reduce wear, minimize power consumption, or achieve desired output.
- Reduce Prototyping Costs: Minimize the need for expensive physical prototypes by validating designs virtually.
- Accelerate Time to Market: Speed up the design cycle by quickly iterating and testing designs.
Advanced Topics and Considerations
For sophisticated analyses, developers and advanced users can delve into more specialized aspects of Motion Study:
- Event-Based Motion: Allows you to define sequences of actions based on specific events (e.g., a component reaching a certain position triggers another motor). This is powerful for simulating complex machine cycles.
- Flexible Bodies (FEA Integration): While Motion Study primarily deals with rigid bodies, it can integrate with SolidWorks Simulation. If a component is defined as a flexible body in Simulation, Motion Analysis can account for its deformation under dynamic loads, providing a more realistic stress analysis.
- Motion Loads to SolidWorks Simulation: A critical feature that allows you to export the calculated forces and torques from a Motion Analysis study directly into a SolidWorks Simulation study. This enables you to perform a static or dynamic stress analysis on individual components under the actual operating loads determined by the motion study.
- Expressions and Functions: Use mathematical expressions or built-in functions to define complex motion profiles for motors, varying forces, or spring characteristics. This provides immense flexibility.
- Data Import/Export: Import motion data from external sources or export results for further analysis in tools like Excel or MATLAB.
- API for Motion Study: For even deeper customization and automation, the SolidWorks API extends to Motion Study. Developers can write custom programs (using VBA, C#, or VB.NET) to automate motion study setup, run analyses, extract specific results, and integrate motion data with other applications. This is invaluable for creating specialized analysis tools or automating repetitive motion analysis tasks.
Best Practices for Effective Motion Studies
To maximize the value and accuracy of your SolidWorks Motion Study, consider these best practices:
- Simplify Your Assembly: Remove unnecessary components or features that do not affect the motion. Suppress non-moving parts or use simplified representations to reduce computational overhead.
- Use Proper Mates: Ensure your assembly mates accurately reflect the real-world constraints. Redundant or conflicting mates can lead to solver errors.
- Define Contacts Carefully: Contacts are computationally intensive. Define them only where necessary and use the appropriate contact type (e.g., SolidWorks’ default contact for general interactions, or specific 3D contact for precise force transmission). Adjust material properties (friction, restitution) accurately.
- Set Accurate Material Properties: For Motion Analysis, material properties (density, friction coefficients, restitution) are critical for accurate dynamic results.
- Start Simple, Then Add Complexity: Begin with an Animation or Basic Motion study to verify general movement. Once satisfied, gradually add complexity (e.g., switch to Motion Analysis, add more precise contacts, apply external forces).
- Understand Solver Settings: Familiarize yourself with the solver settings (e.g., frames per second, precision). Higher precision means longer solve times.
- Interpret Plots Correctly: Learn to read and interpret the various plots. Understand what displacement, velocity, acceleration, force, and torque curves indicate about your mechanism’s performance.
- Validate Results: Whenever possible, compare simulation results with theoretical calculations, hand calculations, or physical test data to validate the accuracy of your model and assumptions.
- Iterate and Refine: Motion Study is an iterative process. Use the insights gained from one simulation to refine your design, then re-run the study to evaluate the impact of your changes.
- Document Your Studies: Keep records of your motion study setups, assumptions, and key results for future reference and collaboration.
Conclusion
SolidWorks Motion Study is a powerful and essential tool for modern mechanical design and engineering. It transcends the limitations of static CAD models, allowing designers to virtually test, analyze, and optimize the dynamic behavior of their assemblies. From simple animations for communication to complex dynamic analyses for performance prediction and load calculation, Motion Study empowers engineers to make informed design decisions, identify potential issues early, reduce the need for costly physical prototypes, and ultimately deliver higher-quality, more reliable products to market faster. By mastering the capabilities of SolidWorks Motion Study, developers and designers can truly bring their mechanical designs to life, ensuring they not only look good but perform flawlessly in the real world.