In the intricate world of manufacturing, quality is not merely a desirable attribute; it is a fundamental requirement. Delivering products that consistently meet design specifications, regulatory standards, and customer expectations is paramount for success and reputation. This relentless pursuit of quality often hinges on robust inspection processes. Historically, these processes have been manual, laborious, and prone to human error. However, with the advent of sophisticated software solutions, quality control has undergone a significant transformation. Among these, SolidWorks Inspection stands out as a powerful and indispensable tool, designed to streamline and automate the creation of inspection documentation, thereby revolutionizing the quality control feature within manufacturing workflows.
Table of Contents
The Challenge of Manual Inspection: A Bottleneck in Production
Before delving into the capabilities of SolidWorks Inspection, it’s crucial to understand the inherent challenges associated with traditional, manual inspection methods. Imagine a complex engineering drawing, replete with hundreds of dimensions, tolerances, and geometric dimensioning and tolerancing (GD&T) symbols.
The conventional approach involves a quality inspector manually reviewing this drawing, identifying each characteristic that requires inspection, and then meticulously “ballooning” or numbering these characteristics directly on a printed copy of the drawing.
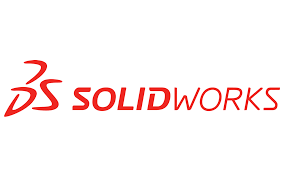
Following this, they would manually transcribe these ballooned characteristics, along with their nominal values and tolerances, into a spreadsheet or a custom inspection report form (such as a First Article Inspection Report – FAIR, or a Production Part Approval Process – PPAP form). This entire process is incredibly time-consuming, tedious, and highly susceptible to errors. A missed dimension, an incorrect transcription, or a misinterpretation of a tolerance can lead to costly rework, scrap, production delays, and even product recalls.
Furthermore, managing revisions of drawings and updating corresponding inspection documents adds another layer of complexity and potential for discrepancies. The sheer volume of data, coupled with the need for precision, often turns manual inspection documentation into a significant bottleneck in the production cycle, hindering efficiency and increasing the risk of non-compliance.
What is SolidWorks Inspection? Empowering Precision and Efficiency
SolidWorks Inspection is a standalone application and a SolidWorks add-in that simplifies and automates the creation of inspection reports and ballooned drawings. It is specifically designed to help manufacturers create First Article Inspection (FAI) reports, in-process inspection sheets, and other quality documentation quickly and accurately. The software addresses the shortcomings of manual methods by leveraging the digital design data and intelligent automation.
At its core, SolidWorks Inspection aims to bridge the gap between design and quality control. By integrating seamlessly with SolidWorks CAD software, it can directly read and extract critical information from SolidWorks drawings. Moreover, its standalone version can work with PDF and TIFF files, making it versatile enough to handle legacy data or drawings from other CAD systems. This flexibility ensures that regardless of the source of the engineering drawing, the inspection process can be standardized and automated.
The primary purpose is to ensure that every critical dimension, tolerance, and note specified in the engineering drawing is captured, measured, and verified against the actual manufactured part. This not only enhances the accuracy of the inspection process but also significantly reduces the time and effort traditionally required for documentation, allowing quality professionals to focus more on actual inspection and analysis rather than administrative tasks.
Key Features and Functionality: A Deep Dive
SolidWorks Inspection is packed with features designed to automate and streamline every aspect of inspection documentation.
Automatic Ballooning
One of the most celebrated features is its ability to automatically balloon drawings. Instead of manually circling and numbering each dimension, tolerance, or note, SolidWorks Inspection can intelligently identify these characteristics on a drawing (whether a native SolidWorks drawing, PDF, or TIFF) and apply sequential balloons.
Users have control over the balloon style, size, and numbering sequence, ensuring compliance with various industry standards. This automation alone can save hours of work on complex drawings, eliminating the risk of missing characteristics or mislabeling.
Characteristic Extraction
The software excels at extracting critical characteristics. It can automatically pull out nominal values, plus/minus tolerances, limit tolerances, and GD&T (Geometric Dimensioning and Tolerancing) information directly from the drawing. For native SolidWorks drawings, it leverages the intelligence embedded in the CAD model.
For PDFs and TIFFs, its powerful Optical Character Recognition (OCR) capabilities come into play, allowing it to “read” the dimensions and tolerances from scanned or raster images. This extraction is highly accurate and significantly reduces manual data entry errors.
Inspection Project Creation
SolidWorks Inspection facilitates the creation of comprehensive inspection projects. Users can define project properties, such as part number, revision, inspector name, and customer details. They can specify the type of inspection (e.g., FAI, in-process, dock audit) and select the specific characteristics to be included in the report. This structured approach ensures that all necessary information is captured for complete traceability and compliance.
Customizable Templates
Compliance with industry standards like AS9102 (Aerospace First Article Inspection Report) and PPAP (Production Part Approval Process) is critical for many manufacturers. SolidWorks Inspection comes with pre-built, customizable templates for these and other common inspection forms.
Users can also create their own custom templates to match their company’s specific reporting requirements, branding, and data fields. This flexibility ensures that the output reports are not only accurate but also professional and tailored to specific needs.
Data Export
The software offers robust data export capabilities. Inspection data, including ballooned drawings and characteristic lists, can be exported to various formats. This includes industry-standard Excel spreadsheets, which are widely used for further analysis or integration with other quality management systems.
Furthermore, ballooned PDFs can be generated, making it easy to share inspection plans with suppliers or shop floor personnel. The ability to export directly to CMM (Coordinate Measuring Machine) programs can also streamline the measurement process by pre-populating CMM software with the required inspection points.
Revision Management
Design changes are an inevitable part of the product development lifecycle. SolidWorks Inspection simplifies revision management. When a drawing revision occurs, the software can quickly compare the new revision with the previous one, highlighting changes in dimensions, tolerances, or notes.
It can then automatically update the inspection project, re-balloon the drawing, and flag any characteristics that have been added, removed, or modified. This ensures that inspection plans remain synchronized with the latest design, preventing costly errors due to outdated documentation.
Optical Character Recognition (OCR)
For companies dealing with legacy drawings or those received in non-native formats (like scanned PDFs or TIFF images), the built-in OCR functionality is a game-changer. SolidWorks Inspection can “read” dimensions, tolerances, and notes from these raster images, converting them into editable data. This eliminates the need for manual re-entry of data from old drawings, significantly speeding up the process and reducing errors.
Integration with CMM Data
SolidWorks Inspection Professional takes integration a step further by allowing the import of CMM measurement data. After parts are measured on a CMM, the results can be imported directly into the inspection project. The software then automatically compares the measured values against the nominal values and tolerances, instantly highlighting out-of-tolerance conditions. This provides a quick visual indication of part quality and streamlines the analysis of measurement results.
Reporting
Generating clear and comprehensive reports is a core function. SolidWorks Inspection allows users to create customizable reports that can include ballooned drawings, characteristic lists, measurement results, pass/fail indicators, and even images. These reports can be visual, making it easy for anyone to understand the inspection results at a glance. The ability to generate professional, accurate, and standardized reports is crucial for compliance, internal communication, and customer satisfaction.
Workflow in SolidWorks Inspection: A Step-by-Step Process
Understanding the workflow in SolidWorks Inspection helps illustrate its efficiency:
- Open Drawing/PDF: The process begins by opening the engineering drawing. This can be a native SolidWorks drawing, a PDF, or a TIFF image. If it’s a PDF or TIFF, the OCR engine will process it to recognize text and dimensions.
- Extract Characteristics: SolidWorks Inspection automatically identifies and extracts dimensions, tolerances, and GD&T. Users can review the extracted characteristics, make any necessary adjustments, or manually add characteristics that might have been missed (e.g., specific notes or non-dimensional requirements).
- Ballooning: With a single click, the software automatically applies sequential balloons to all extracted characteristics on the drawing. The ballooned drawing is then ready for use on the shop floor or for sharing with inspectors.
- Add Actual Measurements: Once the physical parts are measured (either manually or using a CMM), the actual measured values are entered into the inspection project. If CMM data is imported, this step is largely automated.
- Generate Reports: Finally, the software generates the inspection report (e.g., FAI, PPAP) based on the chosen template. The report includes all the ballooned characteristics, nominal values, tolerances, actual measurements, and a clear indication of whether each characteristic passed or failed. The report can then be exported as a PDF or Excel file.
This streamlined workflow significantly reduces the manual effort and potential for errors at each stage, from initial documentation to final reporting.
Benefits of Using SolidWorks Inspection: A Transformative Impact
The adoption of SolidWorks Inspection offers a multitude of benefits that profoundly impact a manufacturer’s quality control processes and overall business operations:
Reduced Time and Cost
Perhaps the most immediate and tangible benefit is the significant reduction in time and cost. Automating ballooning, characteristic extraction, and report generation drastically cuts down the hours spent on manual documentation.
This frees up quality personnel to focus on higher-value tasks, such as root cause analysis, process improvement, and actual part inspection, rather than tedious data entry. The time savings translate directly into cost savings through increased efficiency and reduced labor hours.
Improved Accuracy and Consistency
Automation inherently leads to improved accuracy and consistency. By eliminating manual transcription and data entry, the risk of human error is virtually eliminated. Every characteristic is captured precisely as it appears on the drawing, and every report follows a standardized format, ensuring uniformity across all inspection documentation. This consistency is vital for maintaining high-quality standards and for auditability.
Enhanced Compliance (AS9102, PPAP)
For industries with stringent regulatory requirements, such as aerospace (AS9102) and automotive (PPAP), SolidWorks Inspection is an invaluable asset. Its pre-built, customizable templates ensure that companies can generate compliant documentation with ease. This enhances compliance, reduces the risk of non-conformance, and simplifies the auditing process, providing peace of mind for manufacturers operating in highly regulated environments.
Better Communication
The ability to generate clear, visual, and standardized ballooned drawings and reports improves communication throughout the manufacturing supply chain. Shop floor personnel can easily identify which dimensions to measure, and suppliers can quickly understand the inspection requirements. This clarity minimizes misinterpretations and ensures everyone is working from the same, accurate information.
Reduced Rework and Scrap
By ensuring that all critical dimensions are inspected and verified, SolidWorks Inspection helps in early detection of non-conformances. Catching errors during the First Article Inspection or in-process checks prevents these errors from propagating through production, leading to less rework and reduced material scrap. This directly impacts profitability and sustainability.
Faster Product Development Cycle
The efficiency gained in the quality control phase contributes to a faster overall product development cycle. By streamlining inspection documentation, products can move from design to production and then to market more quickly, giving companies a competitive edge. The ability to rapidly generate and update inspection plans in response to design changes also supports agile manufacturing practices.
Who Can Benefit? A Broad Spectrum of Users
SolidWorks Inspection is not just for a single department; its benefits extend across various roles and functions within a manufacturing organization:
- Manufacturing Engineers: Can quickly generate inspection plans for new products or processes, ensuring that the manufacturing process is robust and capable of producing compliant parts.
- Quality Control/Assurance Teams: These are the primary beneficiaries, as the software directly automates their core tasks of creating inspection documentation, performing inspections, and reporting results. It empowers them to manage quality more effectively and efficiently.
- Design Engineers: Can incorporate inspection requirements earlier in the design phase, leading to more manufacturable and inspectable designs. They can also quickly generate preliminary inspection documents for design reviews.
- Suppliers and Customers: Can benefit from clear, standardized inspection documentation, leading to better understanding of requirements, reduced disputes, and improved collaboration. Suppliers can use the ballooned drawings to guide their own inspection processes, ensuring consistency with the customer’s expectations.
SolidWorks Inspection Standard vs. Professional: Choosing the Right Fit
SolidWorks Inspection is available in two versions: Standard and Professional, each offering different levels of functionality to cater to varying needs.
- SolidWorks Inspection Standard: This version focuses on the core capabilities of automatic ballooning and characteristic extraction from SolidWorks drawings, PDFs, and TIFFs. It allows for manual input of measured values and generation of basic inspection reports. This is ideal for users who primarily need to automate the creation of ballooned drawings and FAI reports without direct CMM integration.
- SolidWorks Inspection Professional: This advanced version includes all the features of the Standard version, plus the crucial ability to import CMM measurement data. It can read results from various CMM formats, automatically compare them against nominal values and tolerances, and provide visual pass/fail indicators. This version is essential for companies that heavily rely on CMMs for their inspection processes and want to fully automate the measurement data analysis and reporting. The Professional version significantly enhances the efficiency of post-measurement data processing.
Best Practices for Implementation: Maximizing Value
To fully leverage the capabilities of SolidWorks Inspection, organizations should consider these best practices:
- Comprehensive Training: Ensure all relevant personnel (designers, manufacturing engineers, quality inspectors) receive thorough training on how to use the software effectively. Understanding its features and workflow is key to maximizing its benefits.
- Standardization of Templates: Develop and standardize custom inspection report templates that align with company-specific requirements, industry standards, and customer expectations. Consistent templates ensure uniformity in reporting.
- Integration with Existing Systems: Explore opportunities to integrate SolidWorks Inspection with other quality management systems (QMS), enterprise resource planning (ERP) systems, or statistical process control (SPC) software to create a more cohesive and automated data flow.
- Continuous Improvement: Regularly review inspection processes and the use of SolidWorks Inspection. Gather feedback from users, identify areas for further automation or improvement, and stay updated with new features and releases.
- High-Quality Source Documents: For optimal OCR performance, ensure that scanned PDFs or TIFF images are of high resolution and clarity. Clear, well-defined drawings will yield the best results during characteristic extraction.
Future Trends and Conclusion: The Path Forward for Quality Control
The landscape of manufacturing is constantly evolving, driven by advancements in automation, data analytics, and smart factories. SolidWorks Inspection is well-positioned within this evolution, serving as a critical component of a digital quality ecosystem.
As industries move towards Industry 4.0, the importance of accurate, traceable, and interconnected quality data will only grow. SolidWorks Inspection’s ability to automate data capture and integrate with other systems makes it an indispensable tool for achieving these goals.
In conclusion, SolidWorks Inspection is far more than just a software tool; it is a strategic asset for any manufacturing company committed to excellence in quality control. By transforming a historically manual and error-prone process into an automated, efficient, and highly accurate one, it empowers manufacturers to reduce costs, accelerate production, enhance compliance, and ultimately deliver higher quality products to market.
In an increasingly competitive global landscape, embracing such advanced quality control features is not just an advantage—it is a necessity for sustained success.