Gone are the days of switching between separate CAD and CAM programs. Today’s design-to-manufacturing workflows demand tight integration, real-time automation, and seamless collaboration between engineers and machinists. SolidWorks CAM rises to the occasion by embedding computer-aided manufacturing directly inside SolidWorks, making it easier than ever to go from part to production.
Whether you’re a product designer preparing for CNC milling or a machinist reviewing G-code, this guide will show you how to leverage SolidWorks CAM to close the gap between design and manufacturing—efficiently, accurately, and automatically.
Table of Contents
What is SolidWorks CAM?
SolidWorks CAM is an integrated CAM solution that uses feature-based machining (FBM) to automate toolpath generation directly within the SolidWorks environment. Powered by CAMWorks technology, it enables users to:
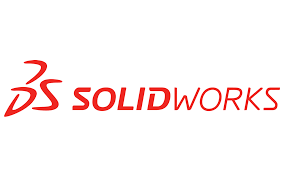
- Generate 2.5-axis and 3-axis toolpaths
- Simulate milling operations
- Export G-code for CNC machines
- Identify machining features automatically
- Customize post-processors for various machines
With SolidWorks CAM, designers and manufacturers work in the same interface—reducing errors, delays, and communication gaps.
Why Use SolidWorks CAM?
✅ Eliminate time-consuming file translations
✅ Create machining operations from your existing CAD model
✅ Automatically recognize pockets, holes, bosses, and slots
✅ Simulate toolpaths in real time
✅ Export verified G-code for CNC controllers
✅ Enable concurrent engineering between design and production teams
SolidWorks CAM brings design and manufacturing under one roof, allowing companies to adopt true model-based definition (MBD) workflows.
Versions of SolidWorks CAM
Version | Features Included |
---|---|
SolidWorks CAM Standard | Part-level machining (2.5-axis milling), FBM, rules-based automation |
SolidWorks CAM Professional | Adds assembly machining, turning, advanced toolpaths, high-speed machining, tolerance-based machining |
Note: CAM Standard is included with every seat of SolidWorks Professional and Premium.
Key Features of SolidWorks CAM
1. Feature-Based Machining (FBM)
Automatically identifies machinable features like:
- Holes
- Pockets
- Bosses
- Slots
Why it matters: Eliminates the need for manual programming and speeds up setup.
2. Knowledge-Based Machining (KBM)
Create rules based on:
- Material type
- Tool availability
- Surface finish
- Tolerance requirements
Why it matters: Repeatable processes = consistent output.
3. Integrated Tool Library
Manage:
- Tool types (mills, drills, reamers)
- Feeds and speeds
- Tool holders
- Toolpath strategies
Why it matters: Reduces human error and helps match shop-floor tools with CAD logic.
4. Setup Wizards
Walk through:
- Machine setup
- Toolpath strategy
- Fixture location
- Coordinate system
Why it matters: Simple for beginners, yet customizable for experienced users.
5. G-code Post Processing
Generate machine-ready code using:
- Built-in post processors
- Customizable output for FANUC, HAAS, Mazak, etc.
Why it matters: No external post-processing software needed.
Common Machining Operations Supported
Operation | Application Example |
---|---|
Facing | Level the surface of a stock material |
Pocket Milling | Create cavities like electronic housings |
Contour Milling | Machine outer edges of parts |
Drilling | Holes for fasteners, bearings, and wires |
Tapping | Threads for mechanical fastening |
Boring | High-precision internal holes |
Chamfering | Deburring sharp edges |
For turning operations, CAM Professional adds:
- Facing
- Grooving
- Threading
- Parting off
Workflow: How to Use SolidWorks CAM
Step 1: Activate CAM
Go to Tools > Add-Ins
→ Check SolidWorks CAM
Step 2: Set Up the Machine
- Choose a default machine (Mill, Lathe)
- Define axis orientation
- Set origin and stock size
Step 3: Feature Recognition
- Auto-detect features using Automatic Feature Recognition (AFR)
- Or create manual features (holes, bosses)
Step 4: Generate Operation Plan
- Assign machining operations (drill, mill, cut)
- Define toolpath strategies (Z-level, raster, contour)
Step 5: Simulate Toolpath
- Use 3D simulation to verify movements
- Check for collisions, overcuts, undercuts
- Analyze material removal
Step 6: Post Process G-code
- Select post processor (e.g., HAAS, FANUC)
- Export
.NC
or.TAP
file - Send to CNC machine for production
Best Use Cases for SolidWorks CAM
Industry | Application Example |
---|---|
Manufacturing | Toolpath programming for production parts |
Product Design | Prototype machining in-house |
Aerospace & Defense | Tolerance-driven manufacturing workflows |
Medical Devices | Small, precise, high-accuracy parts |
Education & Makers | Learning CAM on a real-world platform |
Integration with Model-Based Definition (MBD)
SolidWorks CAM works hand-in-hand with MBD by using 3D annotations like:
- DimXpert dimensions
- GD&T callouts
- Tolerances
It reads these annotations to:
- Apply the correct machining strategy
- Select appropriate tools
- Reduce documentation time
CAMWorks vs SolidWorks CAM
Feature | SolidWorks CAM | CAMWorks (Full) |
---|---|---|
2.5-Axis Milling | ✅ | ✅ |
Turning/Lathe | ❌ (CAM Pro only) | ✅ |
4- and 5-Axis Machining | ❌ | ✅ |
VoluMill Toolpaths | ❌ | ✅ |
Toolpath Editing | Basic | Advanced |
FAQs
Is SolidWorks CAM free?
CAM Standard is included with SolidWorks Professional and Premium. CAM Professional is a paid upgrade.
Can I simulate the machining process?
Yes. SolidWorks CAM includes toolpath simulation with material removal visualization.
Can I use SolidWorks CAM for CNC laser cutting or 3D printing?
No. It’s tailored for subtractive machining (milling and turning). Use SolidWorks Additive Manufacturing Tools or 3rd-party plugins for additive processes.
How accurate is the G-code?
Extremely accurate when the post-processor is correctly configured. Always validate via dry runs and simulations.
Does SolidWorks CAM support 4-axis or 5-axis machining?
Not in the Standard version. You’ll need CAMWorks for full multi-axis capability.
Conclusion: Go from Design to Manufacturing with SolidWorks CAM
SolidWorks CAM bridges the gap between the digital and physical by making CNC programming faster, smarter, and fully integrated. With automated feature recognition, customizable tool strategies, and seamless G-code export, it empowers designers and machinists to collaborate without friction.
No more delays, no more translations—just a direct path from idea to machined perfection.
Suggested
- SolidWorks for Beginners – Complete Getting Started Guide
- How to Use SolidWorks Simulation for Design Validation
- CAMWorks Official Site
- SolidWorks CAM YouTube Tutorials