Introduction
The construction industry has long faced challenges such as delays, budget overruns, miscommunication, and inefficiencies in project execution. Building Information Modeling (BIM) has revolutionized construction project management by integrating 3D modeling with scheduling, cost tracking, and risk assessment to ensure better planning and execution.
With BIM in construction project management, professionals can:
✅ Improve scheduling accuracy with 4D BIM.
✅ Enhance cost estimation and budgeting with 5D BIM.
✅ Reduce construction risks through clash detection and site logistics planning.
✅ Improve collaboration and communication between stakeholders.
This article explores how BIM enhances project management workflows, from planning and scheduling to cost control and risk mitigation.
Table of Contents
What is BIM in Construction Project Management?
BIM in construction project management refers to the integration of intelligent 3D models with project planning, scheduling, and cost estimation tools to optimize construction workflows. Unlike traditional project management methods, BIM enables:
✔ 4D BIM – Links project schedules with 3D models for real-time construction sequencing.
✔ 5D BIM – Adds cost estimation and budget tracking to the project model.
✔ 6D BIM – Includes facility management and lifecycle analysis for post-construction planning.
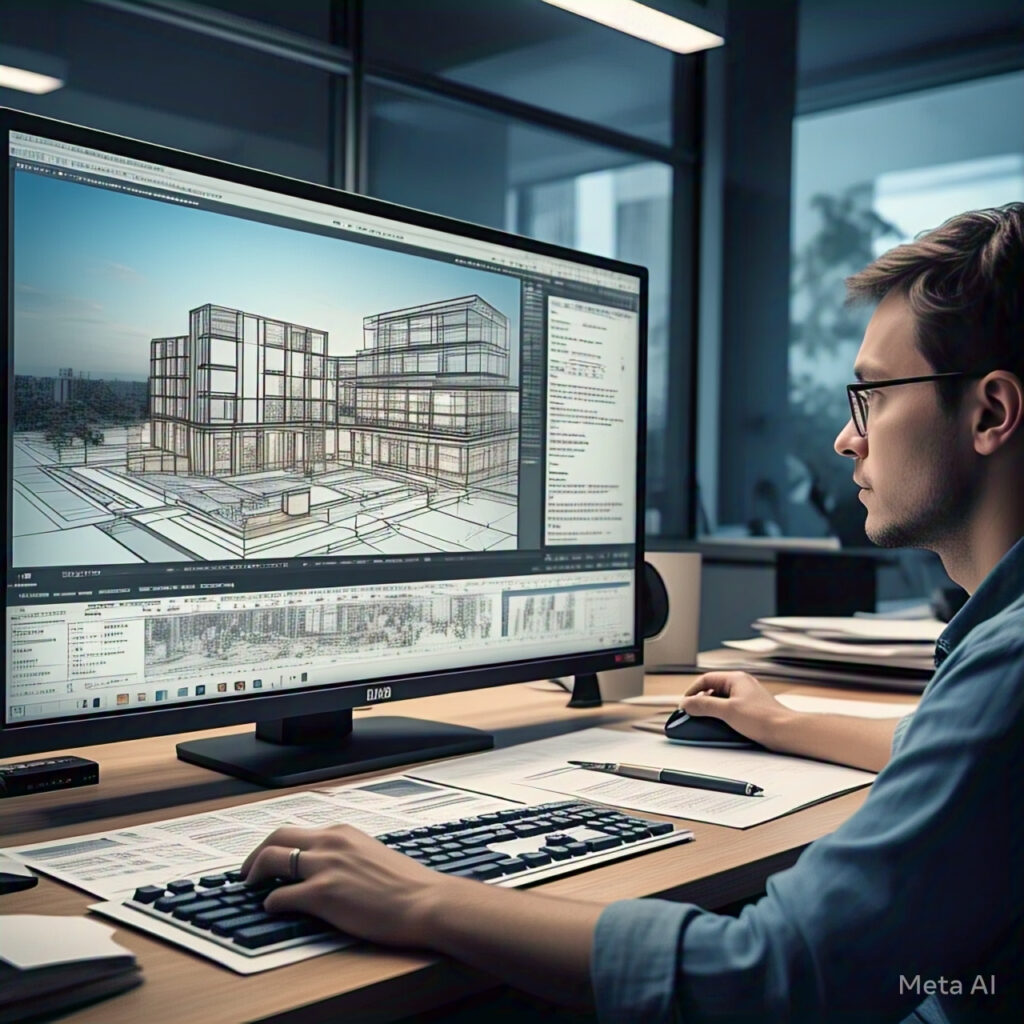
BIM-based construction management is widely used in commercial, residential, and infrastructure projects to ensure efficient coordination, risk reduction, and on-time project delivery.
Key Benefits of BIM in Construction Project Management
1. Improved Project Planning & Scheduling (4D BIM)
BIM enables 4D scheduling, where construction tasks are linked to the 3D model, providing:
- Visual sequencing of project phases, reducing scheduling conflicts.
- Real-time updates that adjust project timelines dynamically.
- Better coordination between contractors, suppliers, and teams.
👉 Example: A contractor using Navisworks Manage can simulate step-by-step construction sequences to identify potential delays and optimize scheduling.
2. More Accurate Cost Estimation & Budgeting (5D BIM)
BIM enhances cost management by integrating real-time material and labor costs into the model.
- Automatically generates quantity takeoffs for cost estimation.
- Tracks material usage to prevent budget overruns.
- Allows scenario analysis for cost-effective alternatives.
👉 Example: A project manager using Autodesk Cost Management in BIM 360 can monitor budget fluctuations in real time and adjust procurement accordingly.
3. Better Risk Management & Safety Planning
Construction risks such as site hazards, structural failures, and scheduling conflicts can be minimized using BIM.
- Simulates construction site logistics to prevent on-site hazards.
- Identifies risks early through clash detection and impact analysis.
- Ensures compliance with safety regulations by modeling emergency routes.
👉 Example: A safety officer using BIM 360 Safety can monitor site conditions and ensure compliance with OSHA standards before work begins.
4. Enhanced Collaboration & Communication
BIM provides a centralized model where all stakeholders can access real-time updates.
- Cloud-based BIM platforms (e.g., BIM 360, Trimble Connect) allow real-time collaboration.
- Reduces miscommunication between architects, engineers, and contractors.
- Ensures project transparency, minimizing change orders.
👉 Example: A construction manager using BIM Collaborate Pro can share models with subcontractors to prevent costly rework.
5. Optimized Material Procurement & Waste Reduction
With BIM-based quantity takeoffs, project managers can:
- Accurately forecast material requirements.
- Reduce overordering, minimizing waste and costs.
- Improve supplier coordination to avoid delays.
👉 Example: A procurement team using BIM 360 Cost can pre-order materials based on model-based takeoffs, preventing excess inventory.
BIM Workflow in Construction Project Management
Step 1: Project Planning & Model Creation
- The BIM model is developed with accurate site data, structural details, and material properties.
- Tools Used: Revit, Archicad, Allplan, Vectorworks
Step 2: 4D Scheduling & Site Logistics
- Construction tasks are linked to the BIM model for visual sequencing.
- Tools Used: Navisworks Manage, Synchro 4D, Primavera P6
Step 3: Cost Estimation & Budget Tracking (5D BIM)
- Quantity takeoffs and cost data are extracted to optimize budgeting.
- Tools Used: BIM 360 Cost, CostX, Trimble Vico
Step 4: Risk Management & Clash Detection
- The BIM model is analyzed to detect structural, MEP, and site coordination issues.
- Tools Used: Solibri Model Checker, Navisworks Clash Detection
Step 5: Construction Execution & Monitoring
- BIM is used for real-time tracking, safety checks, and subcontractor coordination.
- Tools Used: BIM 360 Field, Procore, PlanGrid
Step 6: Handover & Facility Management (6D BIM)
- As-built BIM models are used for maintenance scheduling and asset management.
- Tools Used: FM Systems, Digital Twin platforms
Best BIM Software for Construction Project Management
Software | Best For | Key Features | User Base |
---|---|---|---|
Navisworks Manage | 4D Scheduling & Clash Detection | Model aggregation, visual timeline sequencing | Contractors, BIM Managers |
BIM 360 | Cloud-Based Collaboration | Cost management, issue tracking, field reports | Construction Managers, Owners |
Synchro 4D | Advanced Construction Planning | Time-based simulation, real-time progress tracking | General Contractors, Engineers |
CostX | 5D Cost Estimation | Quantity takeoffs, material tracking, budget forecasting | Quantity Surveyors, Estimators |
Procore | On-Site Project Execution | Document control, site safety management | Project Managers, Site Supervisors |
Solibri Model Checker | Risk Management & Compliance | Rule-based clash detection, quality control | Quality Inspectors, Safety Officers |
Future of BIM in Construction Management
1. AI & Machine Learning for Predictive Analytics
- AI-driven BIM tools will predict project delays and budget overruns before they occur.
2. Digital Twins for Smart Construction Monitoring
- Real-time IoT sensors will connect BIM models to on-site construction activities.
3. Robotics & Automated Construction Using BIM Data
- BIM will guide robotic systems for automated bricklaying, 3D printing, and prefabrication.
4. Augmented Reality (AR) for On-Site BIM Visualization
- AR will allow contractors to overlay BIM models onto real construction sites for better accuracy.
FAQs About BIM in Construction Project Management
1. How does BIM improve construction project scheduling?
BIM links 3D models with timelines (4D BIM), allowing better visualization of project phases and reducing delays.
2. How does BIM help in cost estimation?
BIM provides automated quantity takeoffs (5D BIM), reducing errors and improving budget accuracy.
3. What is the best BIM software for construction project managers?
Popular tools include Navisworks Manage, BIM 360, Synchro 4D, and Procore.
4. Can BIM reduce construction waste?
Yes, BIM optimizes material procurement and prevents overordering, reducing waste and costs.
5. Is BIM mandatory in construction projects?
Many countries require BIM for government and large-scale construction projects to ensure efficiency and cost savings.
Conclusion
BIM is transforming construction project management by improving planning, scheduling, cost estimation, and risk mitigation. Whether managing complex infrastructure projects or residential buildings, BIM ensures efficiency, accuracy, and sustainability.
For construction managers, adopting BIM tools like Navisworks, BIM 360, and Synchro 4D will optimize workflows and enhance project success. 🚀