Introduction
After a building is constructed, managing its maintenance, repairs, and operations becomes a long-term challenge. Facility managers often deal with unorganized documentation, outdated maintenance schedules, and inefficiencies in tracking building assets. Building Information Modeling (BIM) is now transforming post-construction facility management by providing a digital twin of the building with real-time data on assets, maintenance needs, and performance analytics.
By using BIM for facility management, organizations can:
✅ Streamline building maintenance and asset tracking.
✅ Reduce operational costs by improving energy efficiency.
✅ Improve response times for repairs and replacements.
✅ Enhance space utilization and long-term sustainability.
In this article, we will explore how BIM supports facility management, covering practical applications, real-world examples, and best practices for implementation.
Table of Contents
What is BIM for Facility Management?
BIM for facility management refers to the use of intelligent 3D models and data-rich building information to optimize maintenance, repairs, asset tracking, and operational workflows. Unlike traditional paper-based facility management, BIM provides real-time, centralized access to building data for efficient decision-making.
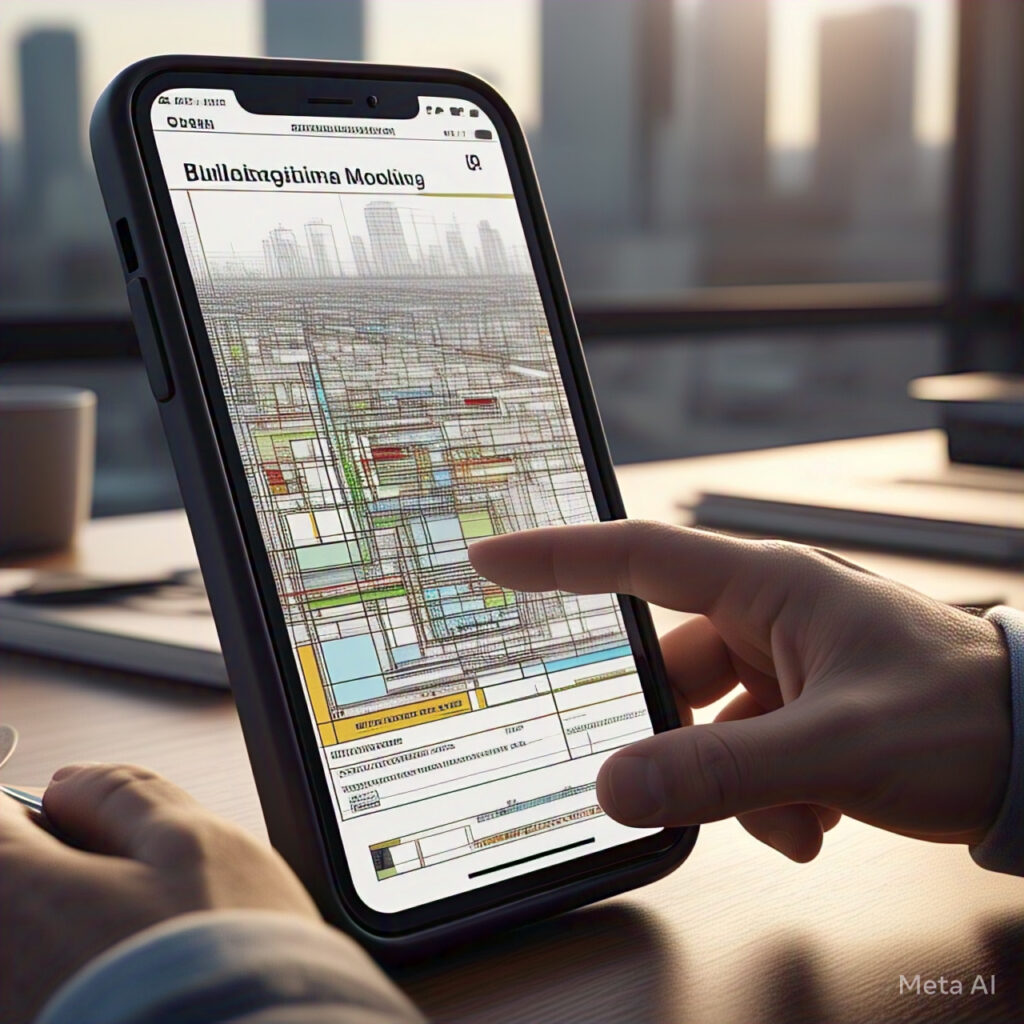
Key Elements of BIM for Facility Management:
✔ As-Built BIM Models – Digital representations of actual building components and systems after construction.
✔ Asset Information & Maintenance Data – Stores equipment details, maintenance schedules, and warranties.
✔ Energy & Performance Monitoring – Analyzes HVAC, lighting, and energy consumption for sustainability.
✔ Space & Occupancy Management – Tracks office layouts, rental spaces, and workspace utilization.
👉 Example: A facility manager using BIM 360 Ops can access real-time data on HVAC system performance, allowing for predictive maintenance and cost savings.
Benefits of BIM in Facility Management
1. Centralized Building Information for Faster Decision-Making
Traditionally, facility managers rely on manual spreadsheets, paper-based maintenance logs, and disconnected databases. BIM provides a single digital model that consolidates all building data in one place.
✔ Instant access to equipment specifications, locations, and maintenance history.
✔ Reduces downtime by providing quick access to system components.
✔ Improves emergency response with detailed floor plans and system layouts.
👉 Example: In a hospital, BIM helps facility managers quickly locate medical gas pipelines and emergency power systems, ensuring faster response times during equipment failures.
2. Predictive & Preventive Maintenance with BIM
BIM enables predictive maintenance, where facility managers proactively schedule maintenance based on real-time equipment performance data rather than reacting to failures.
✔ Identifies potential system failures before they occur.
✔ Extends equipment lifespan by ensuring timely servicing.
✔ Reduces operational costs by avoiding emergency repairs.
👉 Example: A university campus using BIM-based maintenance schedules for HVAC systems reduces annual energy costs by 20% through proactive maintenance and performance tracking.
3. Digital Twins & IoT for Smart Building Management
BIM integrates with Internet of Things (IoT) sensors to create Digital Twins—real-time digital replicas of physical buildings.
✔ Monitors real-time occupancy and air quality.
✔ Tracks energy consumption to optimize efficiency.
✔ Improves space utilization by analyzing room usage patterns.
👉 Example: A corporate office building with IoT-connected lighting and HVAC systems automatically adjusts temperature and lighting based on occupancy, saving energy and improving workplace comfort.
4. Improved Space & Asset Management
Facility managers often need to reorganize office layouts, track rental spaces, or manage storage areas. BIM helps:
✔ Visualize and optimize floor plans for space efficiency.
✔ Manage furniture and equipment locations within the building.
✔ Streamline lease and rental management for commercial properties.
👉 Example: A shopping mall operator uses BIM to track retail spaces, lease agreements, and maintenance schedules, improving tenant satisfaction and revenue management.
5. Enhanced Energy Management & Sustainability
With BIM-based energy analysis, facility managers can:
✔ Monitor heating, cooling, and lighting efficiency.
✔ Identify areas of energy waste and recommend improvements.
✔ Optimize building performance for sustainability certifications (e.g., LEED, BREEAM).
👉 Example: A hotel chain uses BIM for energy modeling to reduce air conditioning costs by 25%, implementing smart energy-saving strategies.
BIM Implementation Strategies for Facility Management
Step 1: Convert As-Built Models to BIM
If BIM wasn’t used during construction, scan-to-BIM technology can create a digital replica of the existing building.
- Tools Used: Autodesk ReCap, Matterport, Leica Geosystems
- Process:
✔ Laser scans capture building geometry.
✔ Data is converted into a 3D BIM model (Revit, Archicad, or IFC format).
✔ Asset data is integrated for facility management.
Step 2: Integrate BIM with Facility Management Software
To maximize efficiency, BIM models should integrate with Computer-Aided Facility Management (CAFM) systems or Integrated Workplace Management Systems (IWMS).
- Popular CAFM & IWMS Platforms:
✔ BIM 360 Ops (Autodesk) – Cloud-based maintenance and asset tracking.
✔ IBM Maximo – Enterprise asset management for large-scale buildings.
✔ Planon – BIM-integrated space and maintenance management.
Step 3: Train Facility Management Teams
✔ Conduct BIM training workshops for facility managers.
✔ Provide on-the-job training on using BIM for maintenance and space management.
✔ Use BIM visualization tools like Navisworks and Solibri for better model navigation.
Step 4: Establish a BIM-Based Preventive Maintenance Plan
✔ Set up automated maintenance schedules for equipment.
✔ Use BIM dashboards to monitor system performance.
✔ Implement IoT sensors for real-time monitoring of HVAC, lighting, and security systems.
Step 5: Track Performance Metrics & Optimize Operations
✔ Measure energy efficiency improvements using BIM analytics.
✔ Track repair response times and maintenance costs.
✔ Use BIM insights to improve future building designs for sustainability.
Challenges in Implementing BIM for Facility Management & Solutions
Challenge | Solution |
---|---|
High Initial Investment | Start with small-scale pilot projects, then expand. |
Resistance to Technology Adoption | Provide training programs for facility management teams. |
Data Integration Issues | Use IFC and COBie formats for compatibility with existing systems. |
Keeping BIM Models Updated | Implement real-time data tracking using IoT and Digital Twins. |
Future of BIM in Facility Management
1. AI-Driven Maintenance & Automation
✔ AI will predict equipment failures before they happen, reducing downtime.
2. Smart Cities & Digital Twins
✔ Large-scale city infrastructure will use BIM & IoT for real-time urban management.
3. Augmented Reality (AR) for Facility Inspections
✔ Facility managers will use AR headsets to visualize building systems in real-time.
FAQs About BIM for Facility Management
1. How does BIM improve facility management?
BIM provides a centralized model for building maintenance, asset tracking, and energy management.
2. What is the best BIM software for facility management?
Popular options include BIM 360 Ops, IBM Maximo, and Planon.
3. Can BIM be used for existing buildings?
Yes, scan-to-BIM technology creates BIM models for older buildings.
Conclusion
BIM is transforming facility management by improving maintenance efficiency, asset tracking, and energy optimization. Organizations that implement BIM-based facility management strategies can reduce costs, improve response times, and enhance building sustainability.
For facility managers looking to modernize operations, adopting BIM tools like BIM 360 Ops, IBM Maximo, and Planon will ensure long-term success and efficiency. 🚀