Introduction
In the realm of computer-aided design (CAD), CATIA (Computer-Aided Three-dimensional Interactive Application) stands out as a premier software suite developed by Dassault Systèmes. Among its myriad of functionalities, the Assembly Design workbench is pivotal for engineers and designers aiming to create complex products by integrating multiple components seamlessly.
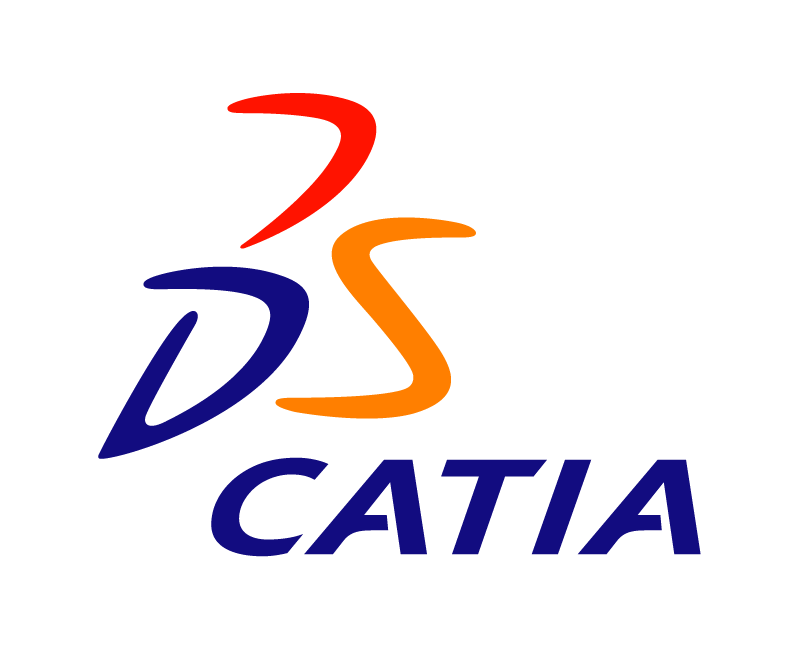
This comprehensive guide delves into the Assembly Design module of CATIA, elucidating its features, advantages, challenges, and best practices. Whether you’re a novice or an experienced user, this article aims to enhance your understanding and proficiency in CATIA’s assembly design capabilities.
Table of Contents
Understanding Assembly Design in CATIA
What is Assembly Design?
Assembly Design in CATIA facilitates the creation and management of assemblies, allowing users to:
- Integrate multiple components: Combine individual parts into a cohesive product structure.
- Define relationships: Establish constraints and connections between components.
- Manage hierarchies: Organize parts and sub-assemblies systematically.
- Simulate real-world behavior: Analyze kinematics and dynamics of assemblies.
Importance in Product Development
In industries like aerospace, automotive, and industrial machinery, products often comprise numerous interconnected parts. Efficient assembly design ensures:
- Accurate fit and function: Components align and operate as intended.
- Reduced errors: Early detection of interferences or misalignments.
- Streamlined manufacturing: Clear guidance for production processes.YouTube
Key Features of CATIA’s Assembly Design Workbench
1. Component Insertion
Users can insert existing parts or sub-assemblies into a main assembly, supporting both bottom-up and top-down design approaches.
2. Constraints Management
Define how components relate to each other using constraints like:
- Coincidence: Aligns faces or edges.
- Contact: Ensures surfaces touch.
- Offset: Maintains a specific distance between elements.
- Angle: Sets angular relationships.
3. Product Structure Browser
Visualize and manage the hierarchical structure of assemblies, making it easier to navigate complex designs.
4. Interference Checking
Detect and resolve clashes between components, ensuring parts fit without overlaps.
5. Kinematic Analysis
Simulate the movement of assemblies to study mechanisms and validate motion paths.
6. Bill of Materials (BOM) Generation
Automatically generate BOMs, detailing components, quantities, and other essential information.
Advantages of Using CATIA for Assembly Design
1. Scalability
CATIA efficiently handles assemblies ranging from simple products to complex systems with thousands of components.
2. Integration with Other Modules
Seamless integration with other CATIA workbenches, such as Part Design and Drafting, ensures a cohesive design process.
3. Parametric Design
Changes in individual parts automatically reflect in the assembly, maintaining design intent and reducing manual updates.
4. Collaboration
Supports concurrent engineering, allowing multiple users to work on different parts of an assembly simultaneously.
5. Visualization Tools
Advanced visualization aids, including exploded views and section cuts, enhance understanding of complex assemblies.
Challenges and Considerations
While CATIA’s Assembly Design workbench offers numerous benefits, users may encounter challenges:
1. Learning Curve
The depth and breadth of features can be overwhelming for beginners, necessitating comprehensive training.
2. Performance Issues
Large assemblies may strain system resources, leading to slower performance without adequate hardware.
3. Constraint Management
Improperly defined constraints can lead to over-constrained or under-constrained assemblies, causing instability.
4. Version Compatibility
Collaborating across different CATIA versions may introduce compatibility issues, requiring careful management.
Best Practices for Effective Assembly Design
To maximize efficiency and accuracy:
1. Plan the Assembly Structure
Before starting, outline the assembly hierarchy, identifying main assemblies and sub-assemblies.
2. Use Naming Conventions
Consistent naming of parts and constraints aids in navigation and reduces confusion.
3. Limit Constraints
Apply only necessary constraints to avoid over-constraining assemblies.
4. Regularly Save and Backup
Frequent saving and versioning prevent data loss and facilitate rollback if needed.
5. Leverage Templates
Utilize existing templates for standard assemblies to save time and ensure consistency.
Real-World Applications
1. Aerospace Industry
Designing aircraft involves integrating numerous systems—structural, mechanical, electrical—requiring robust assembly design capabilities.
2. Automotive Sector
From chassis to interior components, automotive design relies heavily on precise assembly modeling to ensure safety and performance.
3. Industrial Machinery
Complex machinery with moving parts necessitates detailed assembly design to validate functionality and manufacturability.
Conclusion
CATIA’s Assembly Design workbench is an indispensable tool for engineers and designers tackling complex product development. Its comprehensive features facilitate accurate, efficient, and collaborative assembly modeling. By understanding its capabilities and adhering to best practices, users can harness the full potential of CATIA to bring innovative products to life.
FAQs – Assembly Design in CATIA
1. What is the Assembly Design workbench in CATIA used for?
The Assembly Design workbench in CATIA is used to assemble individual parts into a larger product structure. It allows designers to define positional relationships, detect interference, simulate motion, and ensure that all components work together as intended.
2. What are the different types of constraints in CATIA Assembly Design?
Common types of constraints include:
- Coincidence – Aligns edges or surfaces.
- Contact – Ensures surfaces touch.
- Distance (Offset) – Maintains a fixed distance between elements.
- Angle – Defines angular relationships.
- Fix – Locks a part in space.
3. What is the difference between bottom-up and top-down assembly design?
- Bottom-up: Individual parts are designed first and then assembled.
- Top-down: The overall product concept is created first, and individual components are developed within the assembly context.
4. Can I simulate mechanical motion in an assembly using CATIA?
Yes, CATIA supports kinematic simulations that allow users to analyze the movement of parts within an assembly, such as gears, linkages, and other mechanical systems.
5. How can I avoid over-constraining an assembly?
Use only the minimum number of constraints required to define component positions. Over-constraining can cause conflicts and errors. Use the Constraint Diagnosis Tool to detect and resolve constraint issues.
6. Can CATIA generate a Bill of Materials (BOM)?
Yes, CATIA can automatically generate a Bill of Materials for an assembly, listing all components, part numbers, quantities, and other relevant data.
7. Is it possible to reuse components in multiple assemblies?
Absolutely. CATIA supports part reuse, allowing components to be inserted into multiple assemblies without redefining them.
8. How does CATIA handle interference detection?
CATIA includes interference checking tools that detect overlaps or clashes between parts within an assembly, which is critical for ensuring fit and function.
9. What file types are used in CATIA Assembly Design?
The primary file type for assemblies is .CATProduct
, while individual parts use .CATPart
. CATIA can also import/export other CAD formats through plugins and external modules.
10. Can multiple users work on the same assembly in CATIA?
Yes, particularly with CATIA V6 and the 3DEXPERIENCE platform, multiple users can work concurrently on different parts of an assembly using PLM-based collaboration tools.