Introduction
AutoCAD is one of the most powerful and versatile tools used in engineering and manufacturing, especially when it comes to designing mechanical parts. From gears and shafts to fasteners and other machine components, AutoCAD provides the precision and control needed to create detailed 2D and 3D mechanical drawings. In this article, we’ll explore how to use AutoCAD to design various mechanical parts, focusing on essential components like gears, shafts, and fasteners. Whether you’re a mechanical engineer, product designer, or machinist, mastering these techniques will help you produce highly accurate and functional designs.
Table of Contents
Why Use AutoCAD for Mechanical Part Design?
AutoCAD offers several benefits for mechanical part design:
- Precision: AutoCAD allows for exact measurements and geometric constraints, ensuring that parts fit together and function as intended.
- Versatility: With both 2D and 3D design capabilities, AutoCAD allows you to visualize and refine mechanical parts at every stage of the design process.
- Annotation and Documentation: AutoCAD’s annotation tools allow you to add crucial details such as dimensions, tolerances, and materials to your drawings, making it easier to communicate specifications to manufacturers.
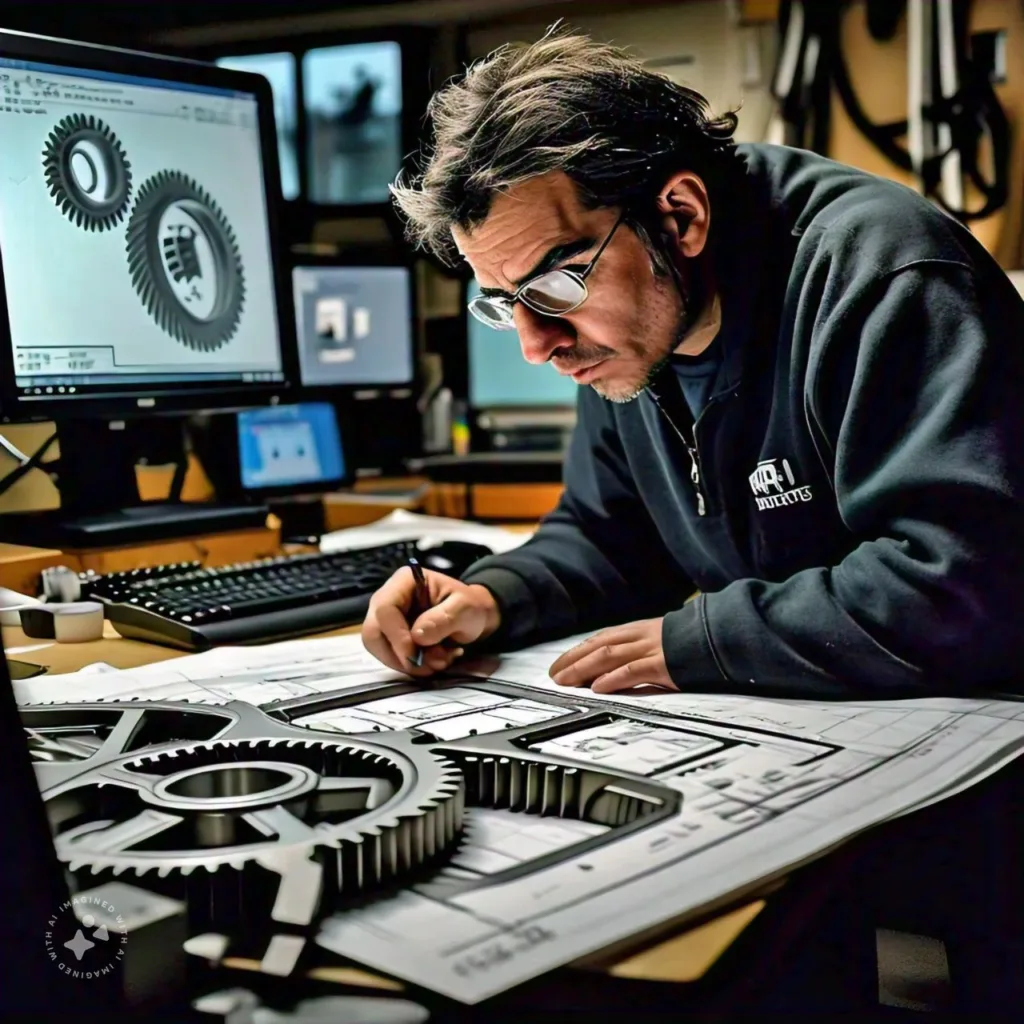
Getting Started with AutoCAD for Mechanical Part Design
Before diving into designing specific parts like gears and shafts, it’s important to set up your AutoCAD environment for mechanical design.
Setting Up Your Workspace
- Switch to the Mechanical Workspace: AutoCAD has a specialized workspace for mechanical design, called AutoCAD Mechanical. This workspace includes tools specifically designed for mechanical parts, making it easier to access libraries, dimensioning tools, and design automation features.
- Go to the Workspace Switching menu in the Quick Access Toolbar and select AutoCAD Mechanical.
- Organize Your Layers: Create separate layers for different components such as shafts, gears, fasteners, and annotations. Layer management is essential for organizing complex mechanical assemblies and making it easier to update or modify individual parts.
Drafting Standards
Mechanical designs must adhere to industry standards to ensure compatibility and safety. Make sure to set up your drawing according to a recognized standard such as ISO, DIN, or ANSI, depending on your industry or project requirements.
- Setting Units: Type
UNITS
in the Command Line and set the drawing units to millimeters or inches, based on the standard you’re following. Ensure precision is set appropriately for your project (e.g., two decimal places for small parts).
Designing Gears in AutoCAD
Gears are one of the most complex yet common mechanical parts. Designing gears in AutoCAD requires precision to ensure proper meshing and functionality.
Step 1: Understanding Gear Terminology
Before you begin, it’s important to understand the key parameters of a gear:
- Pitch Circle Diameter (PCD): The diameter of the pitch circle, where the gear teeth theoretically contact the teeth of another gear.
- Number of Teeth: The total number of teeth around the circumference of the gear.
- Module: The ratio of the pitch diameter to the number of teeth.
- Pressure Angle: The angle at which the gear teeth are cut. Common pressure angles are 20° and 25°.
Step 2: Drawing the Gear Outline
- Calculate Gear Dimensions: Use the module (m) and number of teeth (z) to calculate the pitch circle diameter (PCD). The formula is:PCD=m×zPCD = m \times zPCD=m×zFor example, if the module is 2 and the gear has 20 teeth, the PCD would be:PCD=2×20=40 mmPCD = 2 \times 20 = 40 \, mmPCD=2×20=40mm
- Draw the Pitch Circle: Use the
CIRCLE
command to draw the pitch circle with the calculated diameter. - Draw the Addendum and Dedendum Circles: The addendum circle is slightly larger than the pitch circle, representing the outermost edge of the teeth. The dedendum circle is smaller and represents the base of the teeth.
- Addendum circle diameter: Addendum Circle=PCD+2×Module\text{Addendum Circle} = PCD + 2 \times \text{Module}Addendum Circle=PCD+2×Module
- Dedendum circle diameter: Dedendum Circle=PCD−2.5×Module\text{Dedendum Circle} = PCD – 2.5 \times \text{Module}Dedendum Circle=PCD−2.5×Module
Step 3: Creating Gear Teeth
- Draw One Tooth: Start by drawing a single tooth. Use the
POLYGON
orLINE
tool to create the basic tooth profile. The tooth width should be equal to the module, and the pressure angle can be applied using theANGULAR
constraint. - Pattern the Teeth: Once you have drawn one tooth, use the
ARRAY
command to copy and rotate the tooth pattern around the gear. Set the array to create the correct number of teeth evenly spaced around the pitch circle.
Step 4: Refining the Gear Design
- Fillet the Gear Teeth: Use the
FILLET
command to round off the edges of the teeth, creating a smoother transition between the teeth and the root circle. - Center Bore: Most gears have a center bore for mounting. Draw the bore using the
CIRCLE
command, ensuring the diameter matches the intended shaft.
Designing Shafts in AutoCAD
Shafts are critical components in many mechanical assemblies, transferring power between parts like gears and bearings.
Step 1: Define Shaft Dimensions
Determine the shaft’s length, diameter, and any additional features such as keyways or threads. The diameter of the shaft is often dictated by the load it needs to carry and the gear it connects to.
- Draw the Shaft Profile: Use the
LINE
orPLINE
command to draw the 2D profile of the shaft in side view.- For a cylindrical shaft, simply draw a straight line representing the length of the shaft.
- Extrude the Shaft Profile: Use the
EXTRUDE
command to create a 3D shaft from the 2D profile. Select the profile and specify the extrusion length, which will define the shaft’s length in 3D.
Step 2: Adding Keyways and Threads
- Keyways: Keyways are small slots that prevent rotational slippage between the shaft and the gear or pulley. To create a keyway, draw a rectangle on the surface of the shaft using the
RECTANGLE
command, then subtract it from the shaft using theSUBTRACT
tool. - Threads: To add threads to a shaft, use the
HELICAL
orSWEEP
command. Draw the thread profile and specify the thread pitch and length to create a realistic threaded shaft.
Designing Fasteners in AutoCAD
Fasteners like bolts, screws, and nuts are essential for joining mechanical parts. AutoCAD provides a comprehensive library of standard fasteners that can be inserted into your designs.
Step 1: Inserting Standard Fasteners
- Access the Content Library: AutoCAD Mechanical includes a library of standard fasteners such as bolts, screws, and nuts, following industry standards like ISO and ANSI.
- Go to the Content tab in the Ribbon and select Fasteners.
- Choose the Fastener Type: Select the type of fastener you need (e.g., hex bolt, socket head screw). You can specify the size, material, and thread type based on your design requirements.
Step 2: Customizing Fasteners
- Modify Length or Diameter: Once a standard fastener is inserted, you can adjust its dimensions using the
SCALE
andSTRETCH
commands. This allows you to customize the fastener to fit your specific application. - Threaded Fasteners: For threaded fasteners, you can use the
HELICAL
command to create detailed thread geometry. Alternatively, simplified representations (thread notes) are often sufficient for documentation.
Step 3: Adding Fastener Holes
- Hole Feature: Use the
HOLE
command to create precise holes for fasteners. Specify the diameter and depth of the hole to match the fastener size. - Countersinking and Counterboring: AutoCAD also allows you to add countersinks or counterbores to fastener holes. Use the Hole Editor to define these features, ensuring a perfect fit for the fastener.
Best Practices for Mechanical Part Design in AutoCAD
- Use Geometric Constraints: Ensure that your parts maintain proper relationships by applying geometric constraints such as parallelism, perpendicularity, and concentricity.
- Maintain Design Tolerances: Use AutoCAD’s dimensioning tools to apply tolerances to your parts. This is crucial for ensuring that parts fit together correctly during assembly.
- Check Fit and Function: Use the
MEASURE
andCHECK
commands to ensure that the parts fit together as intended. Perform interference checks if designing an assembly. - Annotate with Precision: Apply detailed annotations, including dimensions, material specifications, and tolerances, to communicate critical design information to manufacturers and engineers.
Conclusion
Designing mechanical parts like gears, shafts, and fasteners in AutoCAD requires a deep understanding of both the mechanical principles and the CAD tools available. By mastering the techniques outlined in this guide, you can create highly accurate, functional mechanical designs ready for manufacturing. AutoCAD’s combination of 2D and 3D design capabilities, along with its powerful annotation tools, ensures that your designs meet industry standards and function as intended in real-world applications.
FAQs
- How do I create gears in AutoCAD?
Use theCIRCLE
command to draw the pitch circle, then create the gear teeth using thePOLYGON
orLINE
tool, and pattern the teeth with theARRAY
command. - Can I design 3D shafts in AutoCAD?
Yes, you can design 3D shafts using theEXTRUDE
command to turn a 2D profile into a 3D object. Add keyways, threads, and other features as needed. - Does AutoCAD have a library of fasteners?
Yes, AutoCAD Mechanical includes a library of standard fasteners such as bolts, screws, and nuts that can be inserted and customized within your design. - How do I apply threads to a shaft in AutoCAD?
Use theHELICAL
orSWEEP
command to create threaded geometry, or apply a simplified representation with annotations. - What are dynamic blocks in AutoCAD, and how are they useful for mechanical design?
Dynamic blocks are reusable objects that can be modified by changing parameters such as size or shape. They save time and improve consistency in mechanical designs.