Introduction
In the construction industry, accurate material estimation is critical for budgeting, procurement, and project planning. Traditionally, quantity takeoff was a manual and time-consuming process prone to human errors. However, Autodesk Revit simplifies this with automated revit quantity takeoff schedules, ensuring efficiency, accuracy, and real-time cost estimation.
With Revit’s parametric modeling, materials, dimensions, and quantities are linked to the Building Information Model (BIM), allowing seamless updates and reducing inconsistencies. This article explores how to use Revit schedules for quantity takeoff, helping professionals create detailed material and cost estimates.
Table of Contents
What is a Quantity Takeoff in Revit?
Definition of Quantity Takeoff
A quantity takeoff (QTO) is the process of extracting material quantities from a BIM model for cost estimation and procurement planning. In Revit, this is done using schedules, which automatically update when the model changes, ensuring real-time accuracy.
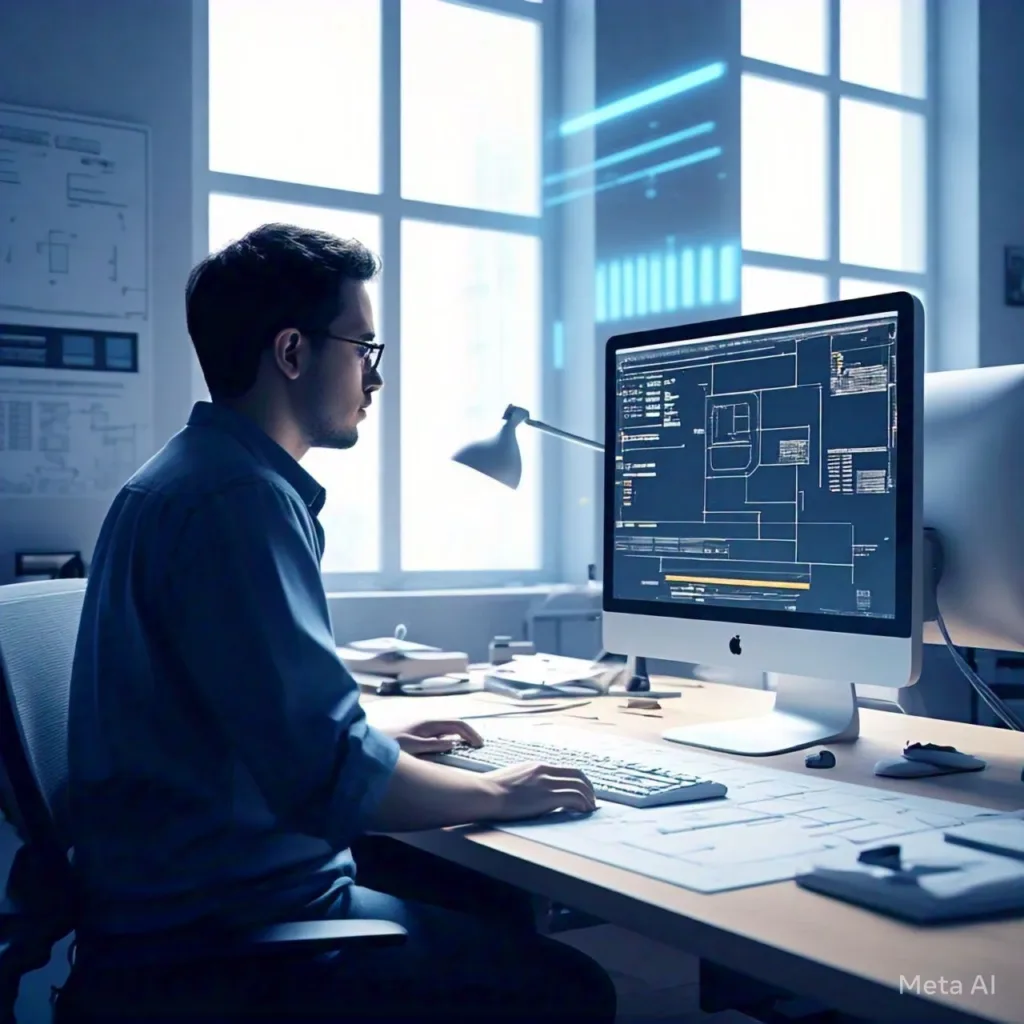
How Revit Schedules Support Quantity Takeoff
Revit schedules enable professionals to:
- Extract material quantities (concrete, steel, wood, etc.)
- Calculate total areas, volumes, and lengths
- Estimate costs by applying unit prices to quantities
- Automate updates when design changes occur
Unlike manual takeoff methods, Revit’s automated schedules eliminate discrepancies and ensure data consistency across all project documentation.
Types of Schedules Used for Quantity Takeoff in Revit
Revit provides multiple types of schedules to facilitate quantity takeoff and cost estimation:
1. Material Takeoff Schedules
Material takeoff schedules extract information about materials used in a project, such as:
- Concrete volume for foundations and slabs
- Steel quantities for beams and columns
- Brick or drywall areas for walls
Example: A concrete schedule calculating cubic meters of concrete needed for a slab.
2. Quantities Schedules
These schedules list the count, area, or volume of specific elements, such as:
- Number of doors and windows
- Total wall surface area for painting
- Length of pipes or ducts in MEP systems
3. Multi-Category Schedules
Multi-category schedules provide a comprehensive breakdown of various materials and components in a single table.
- Example: A schedule displaying doors, windows, and flooring materials in one list.
4. Cost Estimation Schedules
Revit schedules allow users to add cost parameters to calculate total expenses.
- Example: Applying unit costs to a material takeoff schedule to estimate project expenses.
By using these schedule types, project teams can generate highly detailed material and cost reports for budgeting and procurement.
Step-by-Step Guide: How to Perform Quantity Takeoff in Revit
Step 1: Create a New Schedule
- Go to the View Tab → Click on Schedules → Select Schedule/Quantities.
- Choose the category (e.g., Walls, Floors, Doors, Windows).
Step 2: Add Necessary Fields
- Select relevant parameters like Material Name, Volume, Area, Count, Cost.
- Click OK to generate the schedule.
Step 3: Organize and Filter Data
- Apply filters to show only specific materials.
- Sort by material type, cost, or level.
- Group elements (e.g., separating interior and exterior walls).
Step 4: Add Calculations for Cost Estimation
- Add a calculated value column for cost estimation.
- Use a formula:
Total Cost = Material Quantity × Unit Cost
- Ensure unit pricing data is included in material parameters.
Step 5: Format and Export the Schedule
- Adjust column widths, colors, and headers for clarity.
- Export to Excel for further analysis (File → Export → Reports → Schedule).
- Insert the schedule into drawing sheets for documentation.
How to Use Revit for Cost Estimation
1. Assign Unit Prices to Materials
- Edit material properties to include cost per unit (e.g., cost per cubic meter of concrete).
- Create a cost schedule using formulas.
2. Perform Real-Time Cost Updates
- When design changes occur, Revit automatically updates material quantities and costs.
- This prevents budget overruns due to outdated estimates.
3. Link with External Estimation Tools
- Export Revit schedules to Excel or third-party cost estimation software (e.g., CostX, Sage Estimating).
- Use Dynamo scripting for advanced cost automation.
With these strategies, Revit streamlines cost estimation, reducing manual effort and increasing accuracy.
Benefits of Using Revit for Quantity Takeoff
Benefit | Description |
---|---|
Accuracy | Reduces human errors by linking schedules to the 3D model. |
Automation | Updates material quantities automatically when the design changes. |
Efficiency | Saves time by eliminating manual quantity calculations. |
Cost Control | Provides real-time cost insights, helping prevent budget overruns. |
Collaboration | Allows architects, engineers, and contractors to work with the same dataset. |
Challenges in Revit Quantity Takeoff and Solutions
Challenge | Solution |
---|---|
Incorrect Material Assignments | Ensure all elements have correct material parameters. |
Complex Schedule Customization | Use Dynamo to automate complex calculations. |
Formatting Issues | Adjust schedule properties for better readability. |
Limited Cost Data | Integrate with external cost databases or use Excel exports. |
By addressing these challenges, Revit users can maximize the accuracy and efficiency of quantity takeoff.
Best Practices for Revit Quantity Takeoff
1. Maintain a Well-Organized Model
- Assign correct materials and categories to all components.
- Avoid duplicating elements, as this can lead to inaccurate quantities.
2. Use Filters to Simplify Data Extraction
- Apply filters to show only relevant materials (e.g., exclude non-structural walls).
- Sort schedules logically for easy analysis.
3. Validate Schedule Data Before Exporting
- Cross-check material quantities against manual calculations.
- Run a clash detection test to identify inconsistencies.
4. Automate Workflows with Dynamo
- Use Dynamo scripts to automate material takeoff for large projects.
- Create scripts for batch quantity calculations.
By following these best practices, teams can enhance project efficiency and reduce errors in material estimation.
FAQs on Revit Quantity Takeoff
How does Revit calculate material quantities?
Revit extracts material quantities directly from the model, ensuring real-time updates and accuracy.
Can I use Revit for cost estimation?
Yes, by adding unit prices to material parameters and using calculated values in schedules, you can generate cost estimates.
How do I export a Revit quantity takeoff to Excel?
Go to File → Export → Reports → Schedule, then save it as an Excel file for further analysis.
Does Revit support third-party cost estimation software?
Yes, Revit integrates with CostX, Sage Estimating, and BIM 360 Cost Management.
Can Dynamo automate quantity takeoff in Revit?
Yes, Dynamo can automate schedule creation, data extraction, and cost calculations, saving time in large projects.
Conclusion
Revit’s quantity takeoff schedules revolutionize material estimation by ensuring accuracy, automation, and real-time cost analysis. By leveraging parametric modeling, automated updates, and integration with cost estimation tools, Revit provides an efficient and reliable solution for project budgeting.